Exploring the Latest Advancements in Semiconductor Manufacturing Equipment
Are you interested in the semiconductor manufacturing equipment industry? Do you want to learn more about the technology and processes involved in producing these vital components used in electronic devices? You’ve come to the right place.
Here, we will delve into the world of semiconductor manufacturing equipment. We’ll discuss its latest advancements. That way, you can stay up to date with the ever-evolving industry.
So, read on to discover more about the fascinating world of semiconductor manufacturing. Let’s begin!
Extreme Ultraviolet Lithography (EUVL)
One of the most significant advancements in semiconductor manufacturing equipment is Extreme Ultraviolet Lithography. This technology involves using extreme ultraviolet light to print tiny features on silicon wafers. Semiconductor fabrication suppliers like silybwafers.com/ use this process to create the intricate and complex patterns of a microchip.
EUVL has revolutionized the chipmaking process. This is achieved by allowing manufacturers to create smaller and more complex chips. With traditional lithography methods, it becomes increasingly challenging to produce smaller chips. This is because the wavelength of light used for printing limits its resolution.
However, with EUVL, manufacturers can produce chips with finer features and higher density. These of which utilize a much shorter wavelength (13.5 nanometers) compared to traditional lithography (193 nm).
Atomic Layer Deposition (ALD)
The Atomic Layer Deposition process involves depositing ultra-thin layers of material onto a substrate using chemical reactions. ALD has become an essential tool for producing chip components. This includes transistors and capacitors with incredible precision and control.
It allows manufacturers to create films at the atomic level. Thus, resulting in highly uniform and defect-free layers. ALD has enabled the development of new materials, such as high-k dielectrics.
These are crucial for advanced chip designs. This technology has greatly contributed to the miniaturization and performance improvements of electronic devices.
3D Integrated Circuit Packaging
As the demand for smaller and more powerful electronic devices continues to grow, semiconductor manufacturers are turning to 3D integrated circuit packaging. This technology involves stacking multiple layers of chips on top of each other. This is done by placing them side by side on a PCB (printed circuit board).
This method not only saves space. It also offers better performance and power efficiency. With 3D packaging, the distance between components is significantly reduced. Thus, resulting in faster data transfer and lower power consumption.
Plasma Etching Systems
Plasma etching systems are an integral part of semiconductor manufacturing equipment. This process involves using plasma (ionized gas) to remove material from a wafer. Thus, creating the complex features necessary for chip functionality.
With advancements in plasma etching technology, manufacturers can now achieve high levels of:
- precision
- uniformity
- selectivity
All these allow them to produce chips with intricate patterns and structures.
With nanotechnology on the rise, plasma etching systems have become crucial for creating smaller and more powerful chips. Plus, it can etch different materials, such as:
- silicon
- silicon oxide
- metals
All these need the same equipment making it a cost-effective solution for chip production.
Directed Self-Assembly (DSA)
Directed Self-Assembly, or DSA, is a promising technology. It combines the precision of lithography with the self-assembling properties of certain polymers. This process allows for the creation of nanoscale patterns and structures on wafers. This is achieved without using traditional lithography techniques.
DSA has gained attention in the semiconductor industry for its potential to reduce production costs. This is achieved while also increasing chip density and performance.
However, it is still in the early stages of development. Thus, it requires further research and refinement. Moreover, DSA has the potential to revolutionize not only semiconductor manufacturing. It is also for other industries such as healthcare and energy.
Nanoscale Metrology Tools
As the size of semiconductor components continues to shrink, so does the need for high-precision measurement tools. Nanoscale metrology tools are critical in ensuring that chip features meet strict tolerances and specifications.
These tools use advanced techniques such as:
- scanning electron microscopy (SEM)
- atomic force microscopy (AFM)
- X-ray diffraction
All these are used to measure dimensions and properties at the nanoscale level.
SEM
SEM uses electrons to scan the surface of a sample. It produces high-resolution images that reveal information about its topography and composition. It can also be used for measuring feature sizes and defects in semiconductors.
AFM
AFM uses a sharp probe to scan the surface of a sample. It provides 3D images with atomic-scale resolution. This tool is particularly useful for measuring the roughness and thickness of thin films. These are critical parameters in semiconductor production.
X-ray Diffraction
X-ray diffraction is a non-destructive technique that uses X-rays. It helps determine the atomic and molecular structure of materials. It can provide valuable information about:
- crystal structure
- composition
- strain in semiconductor components
Immersion Lithography
Immersion lithography is a method that involves using water as an immersion medium. This is applicable between the lens and wafer. Thus, allowing for smaller feature sizes and increased resolution.
With advancements in immersion lithography techniques, manufacturers can achieve even higher levels of precision at a lower cost. This includes double patterning and multiple patterning.
Multi-Beam Electron Beam Lithography (MBEBL)
Multi-Beam Electron Beam Lithography, or MBEBL, is a novel approach to lithography that utilizes multiple electron beams to expose a wafer simultaneously. This technology offers greater throughput and reduced manufacturing costs. This is evident when compared to traditional single-beam e-beam lithography.
MBEBL also allows for faster mask-writing times. Thus, making it an attractive option for producing chips with smaller feature sizes and higher density.
Chemical Mechanical Planarization (CMP)
Chemical Mechanical Planarization, or CMP, is a critical process in semiconductor manufacturing. It involves smoothing and polishing the surface of wafers to create a flat and uniform substrate for circuit patterning.
With advancements in CMP technology, manufacturers can achieve higher levels of precision and control over wafer surfaces. This can result in improved chip performance and yield.
Computational Lithography
Computational Lithography is a technology that uses advanced algorithms and computer simulations to optimize the lithography process. This approach allows manufacturers to predict and correct any potential issues before printing. This can result in faster production times and higher yields.
Moreover, computational lithography can also help minimize the need for expensive and time-consuming mask revisions. This makes it a cost-effective solution for producing high-quality chips.
Explore the Latest of Semiconductor Manufacturing Equipment
The semiconductor manufacturing equipment industry continues to see significant advancements. As this industry continues to evolve rapidly, professionals and enthusiasts alike need to stay updated.
So, if you are interested in the semiconductor manufacturing equipment industry, be sure to keep an eye out for new advancements.
Should you wish to read more, visit our blog. We’ve got more!
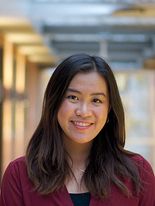
Greetings! I’m thrilled to introduce myself as a dedicated blogger with a fervent passion for crafting meticulously researched and insightful blogs. My mission is to provide you, the readers, with a treasure trove of valuable information. Join me in this exciting adventure of discovery – Thanks